L’IRT M2P se dote d’un nouvel équipement pour la réalisation de pultrudés renforcés
Situées sur le site de Porcelette (57), nos deux lignes de pultrusion permettent la réalisation de pièces à géométrie de section constante. La première ligne de pultrusion est principalement dédiée au développement matériaux (résines et renforts), notamment la résine thermoplastique liquide Elium® élaborée par Arkema.
La seconde ligne, dédiée à des projets R&D applicatifs, se dote d’un nouveau système de tressage investi dans le cadre du projet INFRAlight pour la production de pultrudés composites surtressés. Plus communément désigné sous les termes braid-trusion ou pull-braiding, ce procédé est actuellement utilisé dans différents domaines applicatifs :
- Le BTP : réalisation de barres d’armature ;
- Le secteur ferroviaire : structure de portage et/ou pièces intérieures de train ;
- Le secteur automobile : renforcement de pièces dédiées aux véhicules à hydrogène ;
- L’aéronautique : raidisseur locaux, structures pour sièges.
Grâce au mouvement circulaire de 48 fils autour de l'axe de tressage, ce nouvel équipement permet la conception de pultrudés renforcés transversalement via l’ajout de ces fils entrelacés et orientés sur le contour du profilé. La texturation obtenue par le procédé de tressage permet un état de surface singulier et de répondre à des sollicitations hors plan. Il est également possible de faire varier l’angle de tressage. Les pièces composites induites voient ainsi leurs propriétés mécaniques transverses augmenter de manière significative.
Le procédé de tressage permet la mise en œuvre d’une grande variété de fibres textiles (verre, carbone, fibres naturelles) mais aussi des fibres plus techniques telles que le Kevlar®, ou encore le Dyneema®, fibre de polyéthylène ultra résistante.
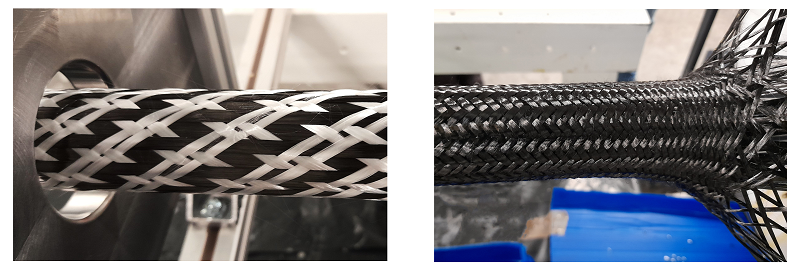
Les bénéfices du tressage
- Le procédé peut être complètement intégré dans une ligne de fabrication et, automatisé ;
- Les structures textiles obtenues sont contrôlables et reproductibles, permettant un niveau de qualité constant et une diminution du coût de renforcement de la pièce ;
- L’augmentation de la résistance mécanique hors axe de production par le biais du tressage sur une couche externe ;
- La technologie de tressage se présente comme une alternative à l’ajout traditionnel de textile type NCF ou tissu dans le procédé de pultrusion ;
- Le procédé offre un gain de productivité et une réduction des coûts grâce au chargement par bobine, supprimant ainsi une étape de transformation de la matière première.
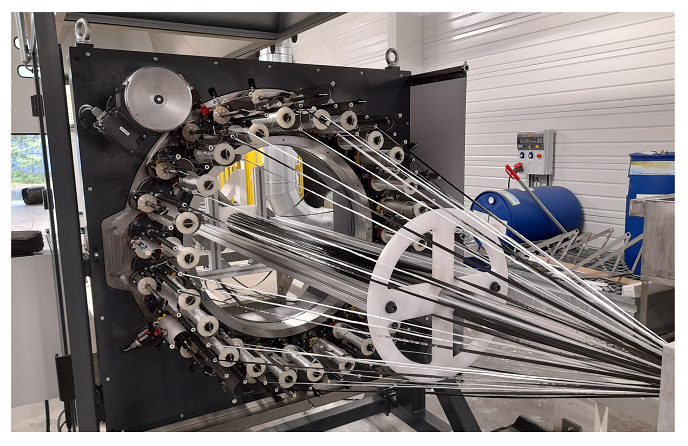
En savoir plus sur le projet INFRAlight
Opéré par l’ADEME, INFRAlight s’inscrit dans le contexte de décarbonation des mobilités et vise la réhabilitation et l’exploitation de lignes de dessertes fines du territoire français. Le projet ambitionne de créer des voies ferroviaires légères en matériaux composites et connectées, adaptées à tout type de trains légers, peu coûteuse en investissements et en exploitation grâce à :
- Un système de rails et entretoises composites recyclables, ancrés au sol par un réseau de pieux verticaux ;
- Une solution de communication intégrée au rail pour l’interaction avec les infrastructures de signalisation et de circulation (passage à niveau, aiguillage) ;
- Un jumeau numérique permettant une maintenance prédictive en temps réel ;
- Une moindre consommation de ressources et de produits manufacturés réduisant l’empreinte carbone.
L’ensemble de cette infrastructure a pour objectif de diminuer drastiquement les coûts de mise en œuvre et d’exploitation afin de permettre un renouvellement des voies de desserte fine tout en réduisant l’empreinte carbone et la consommation de ressources naturelles par l’absence de rails en acier, traverses et ballast et la réutilisation de rails existants.
INFRAlight en chiffres :
- 1 opérateur : ADEME
- 8 partenaires académiques et industriels : CLEARSY, CQFD Composites, EGENIE - Groupe NGE (coordonnateur), IMT Alès, IMT Mines Albi, IMT Nord Europe, INSA, IRT M2P
- 66 mois
- 4 lots couvrant de l’état de l’art jusqu’aux prototypes opérationnels préindustriels
- 13,3 millions d’€